Immersion Cooling Plate is a core component of the liquid cooling system. It is designed for high-power density electronic devices (such as AI servers, GPU clusters, and energy storage batteries). It immerses the heat-generating components directly in non-conductive coolant to achieve efficient thermal management. Immersion Cooling Plate (using precision fluid channels and high thermal conductivity materials, combined with CNC processing technology, can accurately control the heat dissipation path and reduce the chip temperature by 30%-50%, becoming the preferred thermal management solution for data centers, supercomputing centers, and new energy fields.
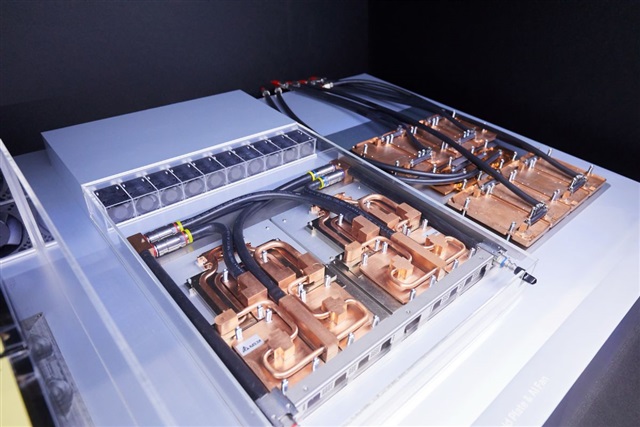
CNC precision machining technology enables cooling plate performance
As a CNC precision machining manufacturer, KingKa ensures the efficiency and reliability of immersion cooling plates through the following processes:
Five-axis linkage precision milling
Using high-rigidity five-axis CNC machine tools, micron-precision fluid channels (width 0.5-2mm) are machined on copper/aluminum alloy substrates to achieve turbulent enhanced heat exchange.
Complex flow channel topology optimization design, such as bionic serpentine or fractal structure, achieves uniform flow distribution through CAM programming, and reduces pressure drop by 40%.
Deep hole drilling and surface carving
For high aspect ratio heat sink fins (depth 50mm, wall thickness 0.8mm), the gun drilling process is used to ensure that the hole wall roughness Ra≤0.8μm and reduce flow resistance.
Surface micro-texturing processing (such as laser etching or CNC carving) increases the specific surface area by 20%-30% and improves the phase change heat transfer efficiency.
Thin-wall structure processing and stress control
The flatness of the ultra-thin base plate (thickness 1-3mm) is controlled to ≤0.02mm to avoid contact thermal resistance.
Through cutting parameter optimization (such as feed rate 0.01mm/rev) and aging treatment, the residual stress of processing is eliminated to ensure long-term sealing.
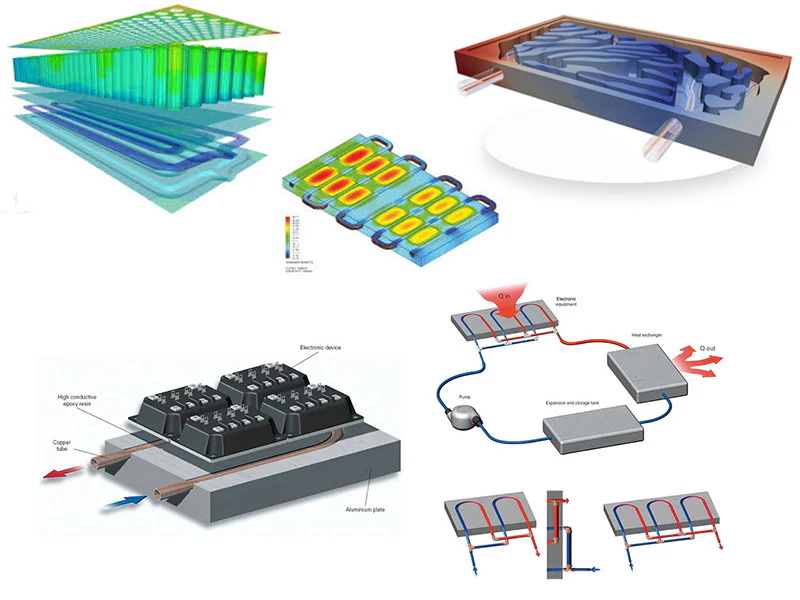
Material and surface treatment technology
Substrate selection
High thermal conductivity metal:
Copper (C1100, thermal conductivity 398W/m·K): used for GPU cold plate and chip-level heat dissipation.
Aluminum alloy 6061/5052 (thermal conductivity 160-200W/m·K): lightweight and cost-effective, suitable for rack-level liquid cooling system.
Special alloy: titanium alloy (corrosion-resistant) or stainless steel 316L (strength > 520MPa), used for offshore platforms or chemical scenes.
Surface modification technology
Micro-arc oxidation: Generate a 10-30μm ceramic layer on the surface of the aluminum substrate, with a hardness of >1500HV and resistance to fluorine liquid corrosion.
Chemical nickel plating: The copper substrate coating thickness is 5-8μm, and the surface resistance is<0.1ω·cm, which="" prevents="" electrolytic="" corrosion.="">
Anodizing coloring: Black or blue oxide film (thickness 8-15μm) improves the radiation heat dissipation rate and meets the aesthetic requirements.
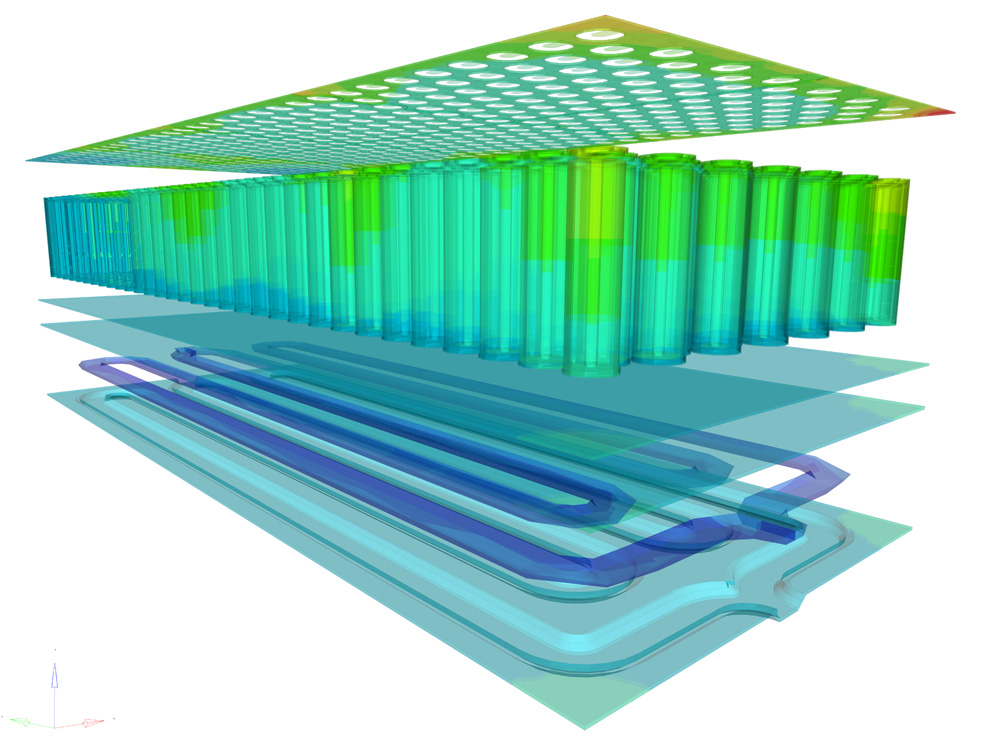
Application fields and scenarios
Data center and AI computing power cluster
Support high-density deployment of 50kW/cabinet, and PUE can be reduced to below 1.05, suitable for AI servers such as NVIDIA HGX H100 and AMD MI300X.
New energy and energy storage system
Power battery immersion heat dissipation: temperature difference control ≤3℃, support 4C fast charging (such as CATL Kirin battery).
Photovoltaic inverter heat dissipation: At an ambient temperature of 60℃, the IGBT junction temperature is reduced by 25%.
Special industrial equipment
Semiconductor laser cooling: through two-phase flow design, heat flux density> 500W/cm².
Military electronics: -40℃~150℃ wide temperature range stable operation, meet GJB150 standard.
KingKa manufacturing advantages: relying on CNC precision processing and material innovation, we provide one-stop service from design simulation (ANSYS Fluent flow channel optimization) to mass production delivery, with tolerance control of ±0.01mm and leakage rate<10⁻⁶pa·m³>